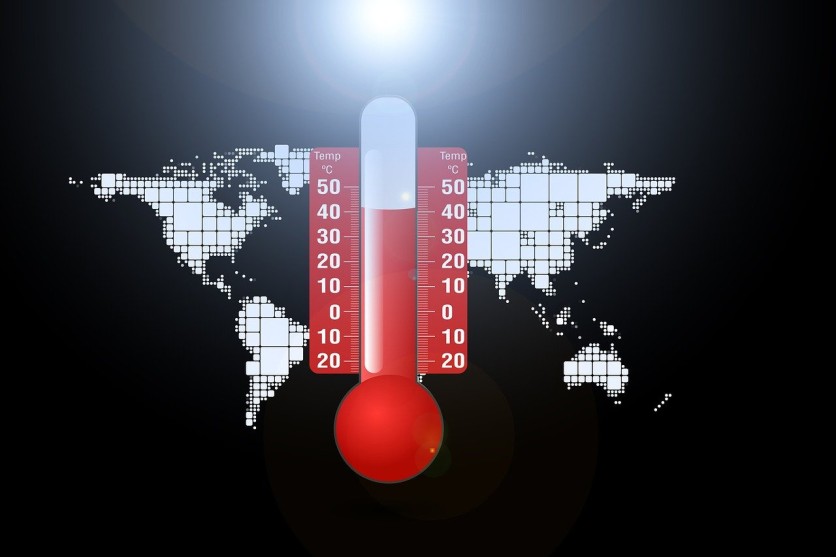
Last year was the warmest on record, and 2024 is already off to a hot start. Meanwhile, local, national, and international climate targets are looming, and moving away from fossil fuels is proving difficult. The U.S., for instance, is projected to fall well short of its 2030 goals for reducing carbon emissions.
One of the barriers to meeting those goals, experts say, comes from the materials used by heavy industry, some of which are believed to be critical to a post-fossil fuel future. Steel, for instance, is both a major source of carbon, making up 9% of global emissions, and a necessary component in things like wind turbines and batteries.
There is some consensus that we need new or improved materials that are easier to produce and possess improved strength and versatility—traits required to harness renewable energy sources. Creating new materials, though, has traditionally been a labor-intensive, time-consuming, and wasteful undertaking.
New Materials to Combat Climate Change
Creating new materials and qualifying them for use in critical components is traditionally a process that takes 10–20 years. But, the materials industry is in the midst of a kind of revolution, according to a recent article by Jiadong Gong at QuesTek Innovations, a materials engineering firm based in the Chicago area.
"Many companies are still using technology from 50 years ago for materials development, which is astounding considering that computing power doubles every 18 months now," Gong writes in Industry Today.
The key is digital transformation, which has become a major factor in many industries looking to introduce efficiencies that will impact the environment and the bottom line.
"Integrating sustainability into a digital transformation program is not just about reducing environmental impact," Chris Weston, a digital services specialist for Jumar, recently told Environment Journal. "It's about future-proofing your business, enhancing efficiency, and meeting the expectations of customers and stakeholders in an increasingly eco-conscious world."
That is the case in the materials world, where digital transformation means using digital models when creating new materials, rather than the traditional and inefficient trial-and-error process that dominated materials engineering through the 20th century.
New Digital Tools for Materials Engineering
Using digital models based on the laws of physics to design new materials isn't anything new. The practice is known as integrated computational materials engineering (ICME), a discipline pioneered by QuesTek co-founder and MIT professor Gregory Olson. ICME has been used by materials engineers for years to create stronger and more versatile materials.
What's different now, writes Gong, is that digital modeling can now be done faster and by organizations that previously wouldn't have found it cost-effective to have a large team of materials engineers on staff. Fueling this shift is the recent proliferation of artificial intelligence and the development of new tools that make a wider range of physics-based digital models more accessible.
"The tools of materials creation can now be wielded by innovative industry players who fully embrace the digital transformation," he writes in Industry Today.
Products in the space include Ansys Granta MI, which can help users manage materials data; Siemens NX, which speeds up the design process using digital twin technology; and ICMD, a SaaS application developed by QuesTek that allows users to bring ICME capabilities in-house, supercharging the ability to develop, design and deploy novel materials.
ICMD and the Democratization of Materials Design
ICMD, which was just released last year, has the potential to be a game changer. Companies that license the technology have access to physics-based digital models developed over a quarter century of QuesTek projects for clients, including Apple, Boeing, and GM, and bolstered by AI and machine learning.
"Nobody has the time and the money to go and melt hundreds of prototype materials and test them one at a time and say, aha, we found the one that works," QuesTek president Jason Sebastian told Design News shortly after the launch of the software. "It's better, compared with the old trial and error approach, [to use] this machine learning that narrows things down and then ... a physics-based understanding to really understand what's going on."
Engineers can use ICMD® to see how changes in the composition and manufacturing process, or other variables, will affect properties of a material such as strength, toughness, corrosion resistance and more. This allows for the creation of lighter, more fuel-efficient materials, alloys that eliminate or reduce the need for environmentally harmful rare earth elements, and novel materials that raise the bar on fuel efficiency at power plants.
With these tools, industries can innovate without the barriers to entry. Gong predicts this so-called "democratization" will have major impacts on the shift away from fossil fuels, such as the development of solar panels, hydrogen containment and nuclear fusion, a few areas where the introduction of new materials are essential.
Likely the first area to see dramatic change will be the electric battery industry, where materials only need to catch up to the existing science of sodium-ion and solid-state batteries.
If you look at the buzz around the recent potential breakthrough in superconductors, it's easy to see how one innovation can revolutionize an industry and help change the trajectory of climate change. Materials engineering may be next.
ⓒ 2025 TECHTIMES.com All rights reserved. Do not reproduce without permission.