The Department of Energy's Oak Ridge National Laboratory (ORNL) has successfully employed 3D printing to create large rotating steam turbine blades for power plants, in collaboration with Siemens Technology.
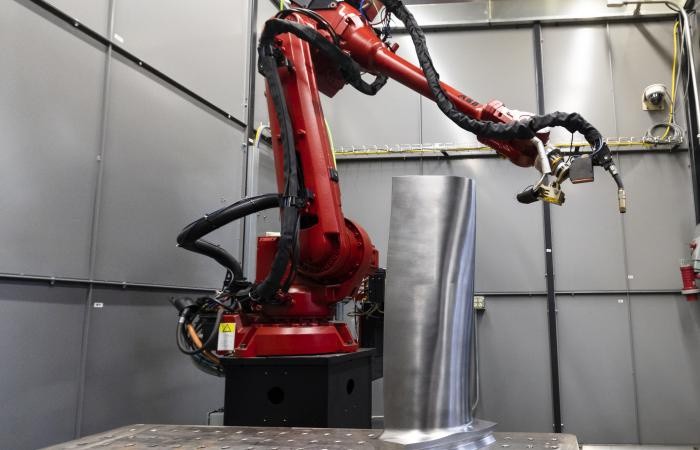
Employing 3D Printing for Power Plants
This achievement marks a significant leap forward in wire arc additive manufacturing, demonstrating its capability to produce crucial components weighing over 25 pounds. Traditionally, these components were manufactured through casting and forging processes, often outsourced internationally.
Interesting Engineering reported that wire arc additive manufacturing utilizes an electric arc to melt metal wire, controlled precisely by a robotic arm. This process builds up thin metal layers to create intricate shapes, subsequently machined to meet final design specifications.
Highlighting the urgency of this breakthrough, Michael Kirka, the lead researcher at ORNL, emphasized the challenge of sourcing low-volume castings and forgings exceeding 100 or 200 pounds domestically.
The collaboration with Siemens Technology, the US-based research and development hub of Siemens AG, aims to tackle the challenges posed by the international movement of critical supplies.
Kirka noted the project's response to an untenable situation, especially given the impact of international conflicts on the movement of essential supplies.
Expanding During Pandemic
While Siemens Technology initially delved into wire arc research for component repair in 2019, the project's scope expanded during the COVID-19 pandemic, driven by the prolonged wait times for new cast steam turbine blades.
In reaction to the challenge, EurekAlert reported that the project expanded its scope to encompass the 3D printing of all replacement parts.
During this expansion, Anand Kulkarni, the senior principal key expert for Siemens Technology, highlighted how the ability to scan the part during the printing process provided crucial information for the machining staff, leading to a reduction in production time.
While traditional methods could stretch over two years, ORNL's 3D printing with wire arc technology allowed the creation of a large steam turbine blade in just 12 hours. With the inclusion of machining, a fully finished blade can be produced within a mere two weeks.
Kulkarni underscored the efficiency of the process, noting that upon recognizing the potential of the wire arc setup at ORNL, the team considered the possibility of manufacturing the entire blade in a single build.
Also Read : This New Ultrasound-Based 3D Printing Tech Could Pave the Way for Less Invasive Surgeries
Wire arc, a well-known 3D-printing technology, found its first application in manufacturing a rotating component of this scale in the project. Kirka acknowledged the challenges, emphasizing the difficulty of printing and finishing without locating features.
After machining, Siemens collaborated with the Electric Power Research Institute on nondestructive evaluation and testing. Kulkarni highlighted the potential for on-demand manufacturing, expressing that the case study opened the envelope to large components.
The ability to 3D-print critical parts not only reduces downtime but also offers a more flexible and reliable alternative to traditional manufacturing methods. An important advantage of 3D printing is liberating companies from dependence on specific manufacturing tools.
Kirka clarified that 3D printing provides a more reliable alternative as it can replicate any design. With many turbine components dating back several decades, the challenge posed by the disappearance of original manufacturing tools is effectively mitigated through 3D printing.
This achievement represents a significant leap forward in energy production, showcasing the transformative potential of 3D printing in the manufacturing landscape.
Related Article : Researchers 3D Print New Superalloy that Could Generate More Electricity with Less Carbon
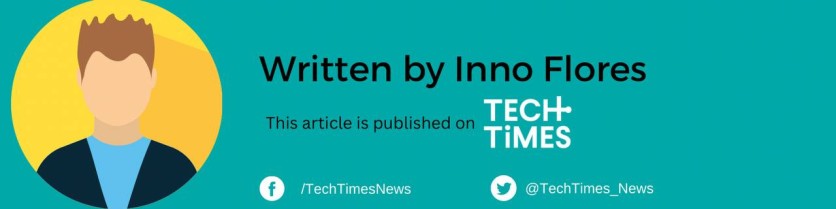
ⓒ 2025 TECHTIMES.com All rights reserved. Do not reproduce without permission.