Structural materials can be produced in novel shapes that were previously impractical with the rise of modern tools such as 3D printers. Its adaptability can be used by emerging generative design techniques to provide fresh designs for various devices.
However, MIT notes that fully automated solutions frequently fall short of creating designs that are optimal for the task at hand since manual design requires a lot of time and labor.
But now, researchers at MIT discovered a technique to combine some of the best aspects of these two methods.
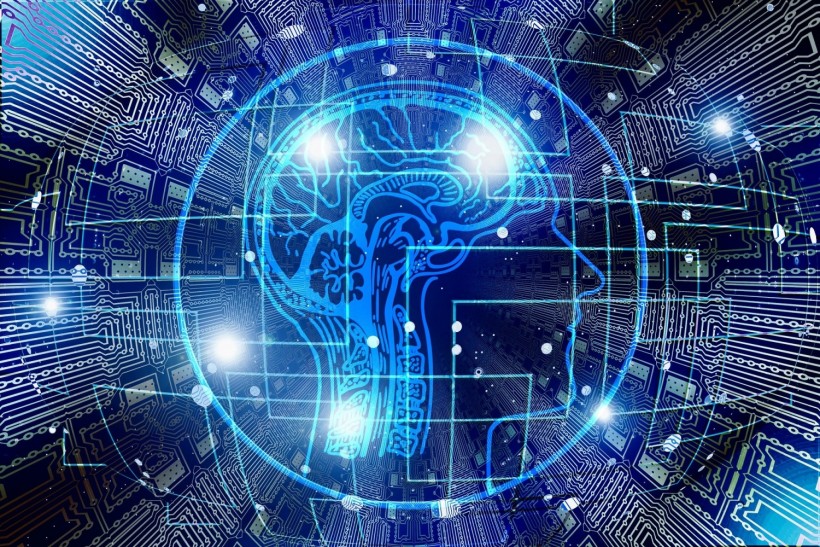
(Photo : Gerd Altmann/ Pixabay)
They employed an automated design system but frequently paused it to let humans review the work in progress and make changes or adjustments before allowing the computer to continue with the design process.
MIT claims that by incorporating a few iterations, the results generated were better performing in contrast to those designed solely by an automated system.
Wide Range of Uses
Josephine Carstensen, a professor of civil and environmental engineering at MIT, claims that the approach can be employed on a wide range of scales and applications. This includes the design of biomedical devices, nanoscale materials, and structural support members of skyscrapers.
Dat Ha, an MIT doctoral student, said that this approach takes advantage of the superior manufacturing capabilities of modern instruments. These tools may enable designers to enhance the performance of their concepts by optimizing them and creating novel shapes that are both lightweight and structurally robust.
To demonstrate their approach, the researchers built a variety of load-bearing beams that are typically seen in structures like houses or bridges. Using their iteration process, they identified a specific area in the design that hat could potentially fail prematurely. They then instructed the computer program to fix the problem.
As a result, the automated system modified the design, deleting the identified strut and replacing it with other struts. This led to a final design that was significantly improved in terms of structural strength and durability.
The procedure, which they refer to as Human-Informed Topology Optimization, starts by defining the requirements, such as that a beam must have this length, be supported on two points at its ends, and support a specific amount of weight.
Carstensen notes that their method entails watching the structure change in response to an initial specification on a computer screen. They stop the design during this step to get user feedback on its suitability.
Read Also: MIT Engineers Devise New Method to Make Protein Drugs Cheaper
AI-Human Design System
The combination of automated design systems with user input may allow for faster and more efficient design iterations while still producing designs that are optimized for their intended purpose.
According to Carstensen, their new approach is not only easy to use and effective on less powerful systems, but it also takes less training to yield useful results.
A basic two-dimensional version of the software that can be used to build simple beams and structural components is currently available online while the team works to create a full 3D version.
The results of the work were published in the journal Structural and Multidisciplinary Optimization.
Related Article: MIT Researchers Propose Direct Carbon Capture from Seawater