NASA engineers have achieved a significant milestone by testing hybrid printed circuits at the edge of space. The experiment occurred during a sounding rocket flight on April 25, launched from NASA's Wallops Flight Facility near Chincoteague, Virginia.
The technology involved printing electronic temperature and humidity sensors on the payload bay door and attached panels, allowing real-time data collection during the SubTEC-9 sounding rocket mission.
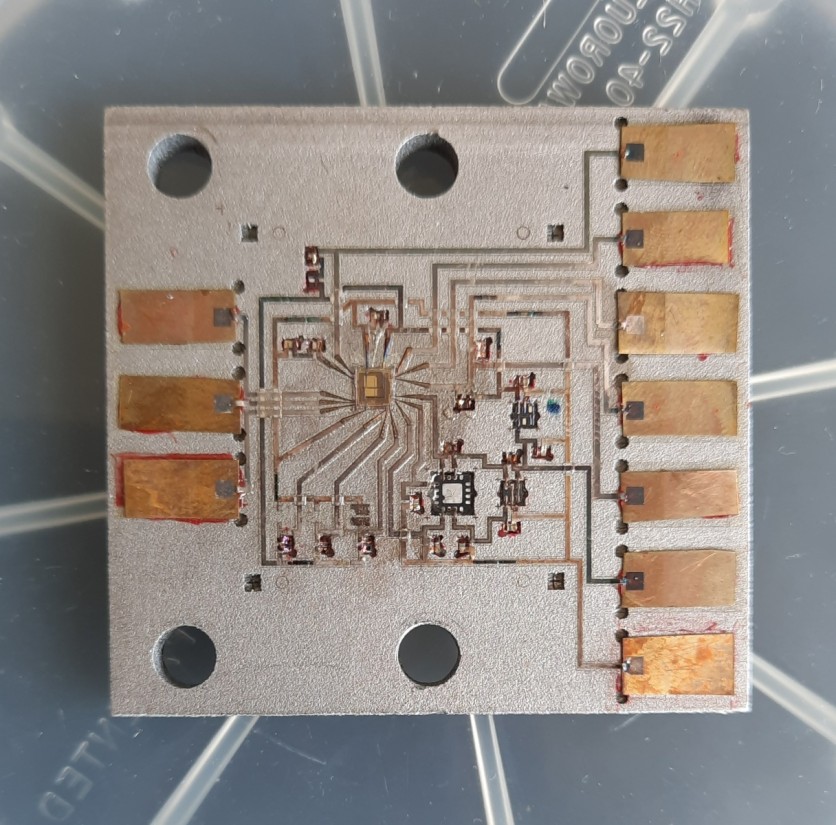
Space-Readiness of Printed Electronics
The experiment was led by aerospace engineer Beth Paquette and electronics engineer Margaret Samuels from NASA's Goddard Space Flight Center in Greenbelt, Maryland.
Their primary objective was to demonstrate the space-readiness of printed electronics technology, which offers the unique capability of printing sensors precisely where they are required.
Samuels emphasized that the technology serves as a space-saving measure, enabling printing on 3-dimensional surfaces with traces as thin as 30 microns, equivalent to half the width of a human hair.
The team collaborated with colleagues from NASA's Marshall Space Flight Center in Huntsville, Alabama, responsible for developing the humidity-sensing ink, along with partners from the University of Maryland's Laboratory for Physical Sciences (LPS).
Together, they successfully created and validated the hybrid printed circuits. The use of printed circuits introduced a new level of functionality for smaller spacecraft, which are increasingly becoming a norm for both near-Earth and deep space missions.
Brian Banks, an electronics engineer at Wallops, explained that this hybrid technology allows circuits to be fabricated in previously inaccessible locations for conventional electronics modules.
Moreover, printing on curved surfaces holds the potential to be beneficial for small, deployable sub-payloads where space constraints are a significant challenge. The experiment marked a turning point in LPS's development and validation of printed-circuit technology.
LPS engineer Jason Fleischer, who designed and printed the circuits for the April flight, used advanced printers capable of generating electronic traces thinner than the human eye can perceive.
Read Also : More Americans Prefer NASA Missions Against Killer Asteroids Instead of Mars Expeditions: Survey
Printing X-Ray Instruments
In a separate investigation, the team achieved a milestone by printing X-ray instruments on flexible Kapton plastic strips, expanding the application of printed electronics to various space missions.
Samuels explained that the team can now print antennas on curved surfaces, such as the exteriors of rockets or spacecraft, enabling improved signal transmission and reception angles in space.
Unlike traditional antenna connections, which involve messy and imprecise wire bonding, the shift to printed connections signifies a significant improvement in stability and efficiency, maximizing the potential of precision antenna technology, according to NASA.
Paquette envisions future missions that could utilize printed temperature sensors throughout a spacecraft's interior surfaces. This cost-effective approach could provide invaluable insights into how heating and cooling affect the spacecraft as it journeys close to celestial bodies like the Sun.
The experiment's success caught the attention of engineer Ryan McClelland at NASA's Goddard Space Flight Center, who pioneers the utilization of "evolved structures," which uses computers and artificial intelligence to design and make spacecraft parts.
Related Article : Are Talking Spaceships Coming Soon? NASA to Revolutionize Space Exploration with AI-Powered ChatGPT-Like Interface

ⓒ 2025 TECHTIMES.com All rights reserved. Do not reproduce without permission.