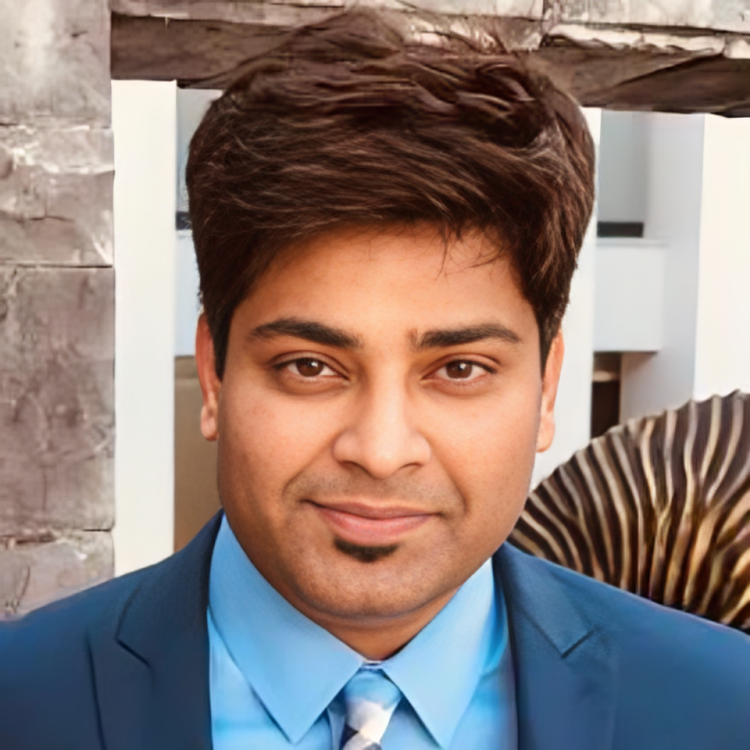
In the ever-evolving landscape of industrial and process plants, the concept of predictive maintenance is rapidly gaining traction as a game-changer. At the heart of this transformation are two powerful technologies: Artificial Intelligence (AI) and the Industrial Internet of Things (IIoT). Together, they enable plants to not only identify production equipment issues but also fix them before they lead to failures and costly downtime. This predictive maintenance revolution is not just a trend; it's a necessity for future-ready facilities that aim to thrive in today's competitive environment.
Sundeep V. Ravande is the CEO of Innovapptive Inc. He is responsible for driving the company's vision to become the #1 Connected Worker experience software provider. According to Sundeep, here are some AI-driven insights for future-ready facilities:
Addressing Pain Points in Industrial and Process Plants
Before delving into the transformative potential of predictive maintenance, let's first understand some of the significant pain points that plague industrial and process plants:
Lack of Operational Visibility: In many facilities, there is a lack of real-time visibility into the status and health of critical production equipment. This blind spot makes it difficult to anticipate issues and respond proactively.
Reactive Maintenance Processes: Traditional maintenance approaches often follow a reactive pattern-repairs occur only after equipment failure. This results in costly downtime, unplanned maintenance, and increased wear and tear on machinery.
Low Frontline Worker Productivity: Frontline workers are often bogged down by cumbersome, manual data collection and maintenance tasks. This inefficiency hampers productivity and prevents them from focusing on value-added activities.
Information Silos: Vital maintenance data is often scattered across disparate systems and departments, creating information silos. This fragmentation hinders effective decision-making and coordination.
AI and IIoT: The Predictive Maintenance Power Couple
Now, let's explore how the combination of AI and IIoT can revolutionize maintenance operations in industrial and process plants:
Real-time Equipment Monitoring: IIoT sensors and devices can continuously collect data on equipment health, performance, and operating conditions. AI algorithms then process this data in real time, identifying anomalies and potential issues before they escalate.
Predictive Analytics: AI-driven predictive analytics leverage historical data, sensor readings, and machine learning models to forecast equipment failures. These insights enable maintenance teams to schedule proactive repairs, reducing costly downtime.
Condition-based Maintenance: Instead of adhering to rigid maintenance schedules, AI and IIoT enable condition-based maintenance. Maintenance is performed when equipment parameters indicate it's necessary, maximizing asset lifespan and efficiency.
Operational Visibility: AI-powered dashboards and reporting tools provide plant managers and operators with a comprehensive view of equipment health and performance. This real-time visibility helps in making data-driven decisions and optimizing operations.
The Mobile-First Connected Worker Platform
To fully harness the potential of AI and IIoT in predictive maintenance, a mobile-first connected worker platform plays a crucial role. This platform empowers frontline workers with the information and tools needed to drive insights and overcome the aforementioned pain points:
Real-time Alerts and Notifications: Mobile devices equipped with the connected worker platform can deliver real-time alerts to frontline workers when anomalies are detected. This ensures rapid response and minimizes downtime.
Streamlined Data Collection: Mobile applications simplify data collection, allowing workers to record equipment readings, observations, and maintenance tasks digitally. This eliminates paperwork, reduces errors, and boosts worker productivity.
Access to Historical Data: Workers can access historical maintenance data, equipment manuals, and repair procedures directly on their mobile devices. This comprehensive information ensures that workers are well-equipped to handle maintenance tasks effectively.
Collaborative Workflows: The connected worker platform facilitates collaboration among team members by enabling real-time communication and knowledge sharing. This breaks down information silos and fosters a culture of continuous improvement.
The ROI of Predictive Maintenance
The benefits of predictive maintenance powered by AI, IIoT, and a mobile-first connected worker platform are substantial:
Reduced Downtime: Proactive maintenance reduces unplanned downtime, ensuring continuous production and minimizing revenue losses.
Lower Maintenance Costs: By identifying issues before they lead to major failures, maintenance costs are significantly reduced, as are emergency repair expenses.
Improved Asset Lifespan: Condition-based maintenance extends the lifespan of critical assets, reducing the need for premature replacements.
Enhanced Productivity: Frontline workers can focus on value-added tasks, and the efficiency gains lead to higher overall productivity.
Safety and Compliance: Real-time alerts and access to safety protocols enhance worker safety, ensuring regulatory compliance and preventing accidents.
The predictive maintenance revolution fueled by AI, IIoT, and mobile-first connected worker platforms is a game-changer for industrial and process plants. By addressing pain points such as lack of operational visibility, reactive maintenance processes, low frontline worker productivity, and information silos, these technologies enable plants to operate efficiently, reduce downtime, cut costs, and improve safety. Investing in predictive maintenance is not just about staying competitive; it's about future-proofing your facility for the challenges and opportunities.
ⓒ 2025 TECHTIMES.com All rights reserved. Do not reproduce without permission.